Quality Assurance
Q-SOLAR has completed its supplier audit, quality assurance and inspection of its supplier factories. We have supply chain experts and senior quality engineers with rich project experience to provide and guarantee the project quality. Our quality assurance service covers the whole production process, from raw material inspection to the customer delivery of assembled solar modules, frames, inverters and other photovoltaics products.
We have many well-proofed QA and inspection schemes to meet the needs and expectations from different customers. We provide our customers with the best quality products through our long-term partnered suppliers and our professional engineering team. Thus the quality of a solar power station in its whole life time is guaranteed and our customer’s ROI (Return of Investment) is increased.
Our quality assurance process is as follows:
- Factory Audit
Q-SOLAR proceeds audits in supplier’s quality system, certifications and licenses, compliance of materials, product design, production equipment, inspection facilities, standard plates, measurement etc.
- Inline Production Monitoring:
Independent engineers conduct 7*24 monitoring on the whole production process from raw material preparation through equipment inspection to storage and final shipment. Main working areas include:
- following and verifying the whole project timeline and schedule.
- verifying daily loading, storage and shipment quantity.
- monitoring the whole module production schedule to ensure its progress.
- conducting random inspection. Independent engineers divide modules into different lots and conducts random inspection based on testing items, ratios and specification to take further deep and intensive control of the overall quality.
- Shipment Inspection:
Q-SOLAR strictly follows the technical standards concluded between customers and suppliers on technology specification, samplings and refers to the international common standards IEC61215/IEC61730 on equipment inspection, including but not limited to :
- Appearance (Visual Inspection)
- EL Testing
- Flash Testing
- Insulation Testing
- Making a decision on whether shipment proceeds or is refused based on sampling testing results
- Shipment Supervision
Q-SOLAR will perform the followings upon each container shipment by the supplier:
- Confirm loading quantity of each container
- Confirm each cargo container is inspected and approved by Q-SOLAR standards
- Confirm the compliance of packaging and product specifications
- Confirm that customer requested information is received etc.
- Sampling Testing
Q-SOLAR can pick on-site samples by random based on customer’s request and perform corresponding testing in professionally licensed institutions (e.g. TUV).
- Final Report
Q-SOLAR provides a final summary report within 10 days after the overall order is shipped. This report covers all the inspection results during the whole process from order beginning to loading completion.
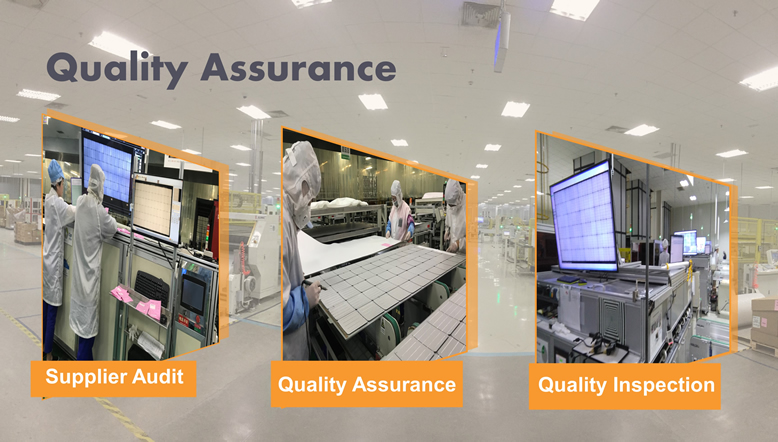